Beton, sauberer in die Zukunft
Beton ist weltweit allgegenwärtig und als Baumaterial eigentlich nicht zu ersetzen. Der Baustoff genießt, was das Klima anbelangt, aber einen schlechten Ruf. National wie international gibt es unzählige Projekte, die das Material klimafreundlicher machen sollen. Neue, stark CO2-reduzierte Zement- und Betonrezepturen drängen laut Forschenden auf den Markt.
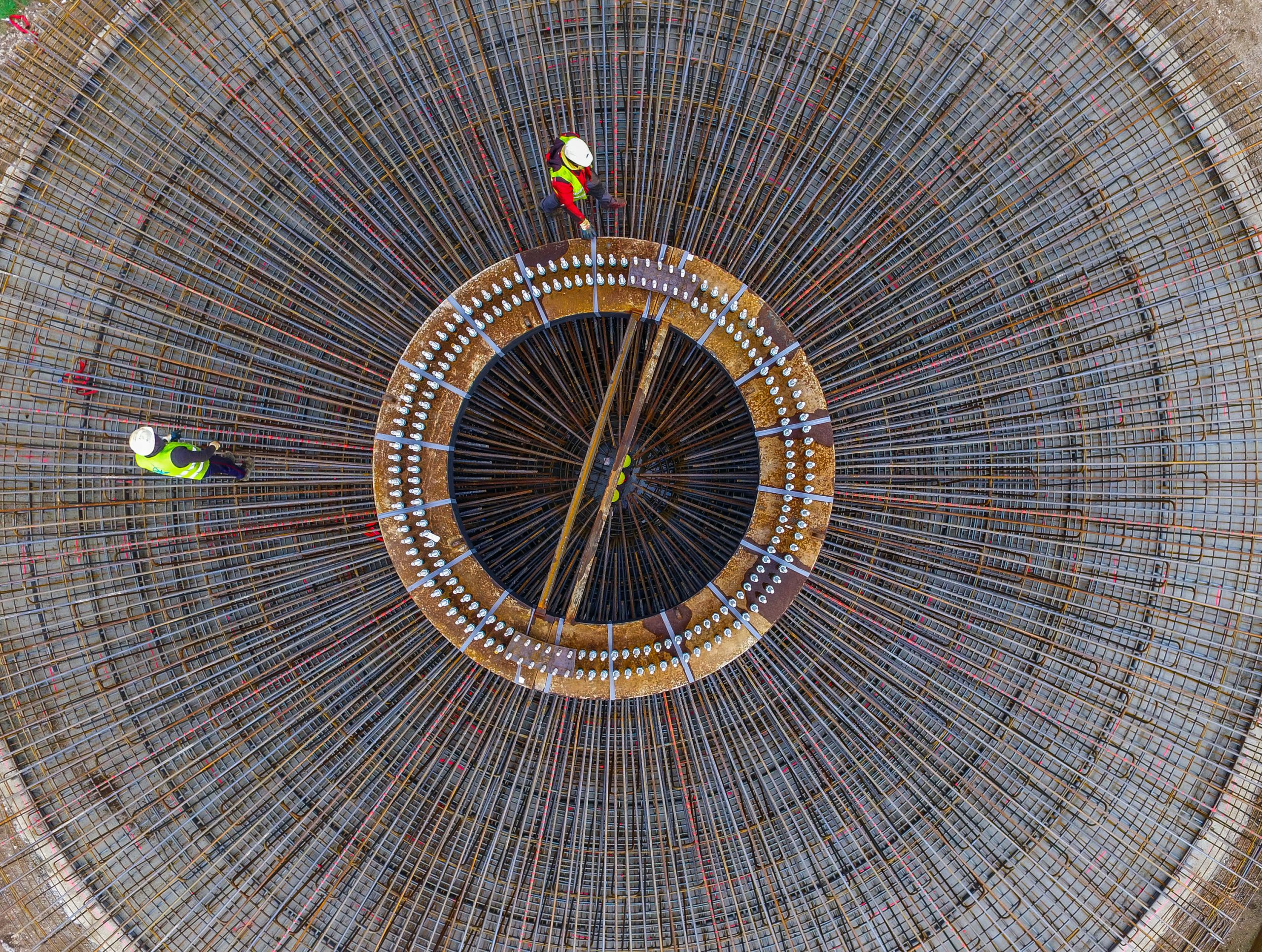
„Beton kann durch keinen anderen Baustoff in großem Maßstab ersetzt werden. Er ist nämlich ein einfaches Material, das leicht, schnell, lokal und ‚technologiearm‘ hergestellt werden kann, ist hoch belastbar und relativ einfach zu verbauen“, beschreibt Ildiko Merta, Materialwissenschafterin am Institut für Werkstofftechnologie, Bauphysik und Bauökologie der TU Wien und Gastprofessorin an der Fakultät für Technische Wissenschaften der Universität Novi Sad (Serbien), warum Beton beim Bauen allgegenwärtig zu sein scheint.
„Beton ist weltweit mit einem Anteil von nahezu 90 Prozent der mit Abstand meist eingesetzte Baustoff“, so Merta weiter. „Laut diversen Prognosen werden global bis 2030 mehr als 25 Millionen Häuser benötigt. Das ist eine immense Herausforderung und Beton als Baustoff wird dabei eine zentrale Rolle spielen müssen“, meint die Wissenschafterin.
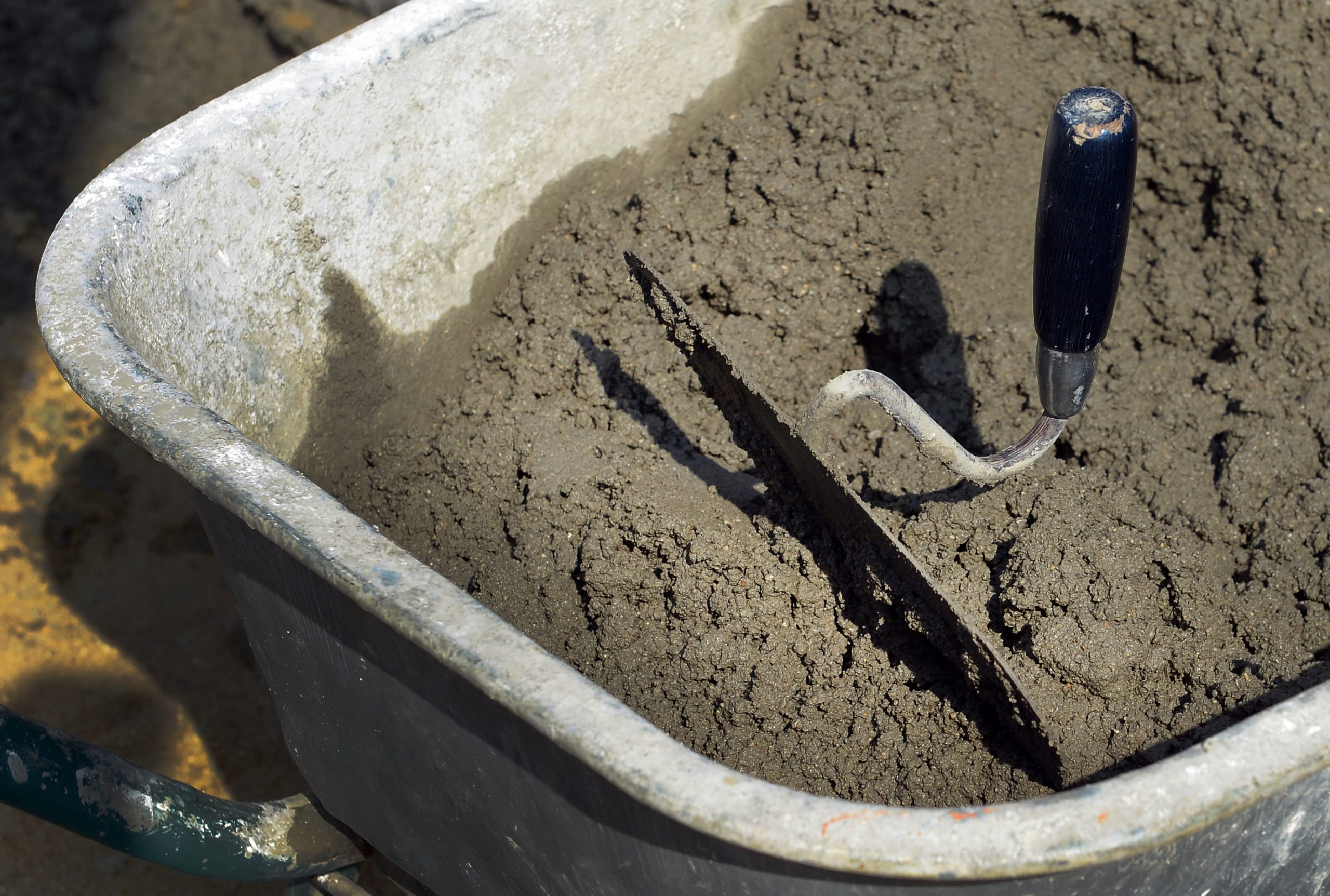
Zementverbrauch wächst stark
Ein zentraler Bestandteil von Beton ist Zement (10 bis 15 Prozent; 60 bis 75 Prozent sind Zuschlagstoffe wie Kies und Sand, 15 bis 20 Prozent Wasser). Geografisch gesehen wird Zement zu 90 Prozent in Entwicklungs- und Schwellenländern genutzt und auch künftig gebraucht. In diesen Regionen hat es die vergangenen Jahrzehnte massive demografische Wachstumsschübe gegeben, was den Zementverbrauch in den letzten 30 Jahren laut Ildiko Merta von der TU Wien stark in die Höhe getrieben hat. Allein China kommt mittlerweile für mehr als 50 Prozent des globalen Zementverbrauchs auf, dahinter folgt Indien. „Von einem weiterem starken Wachstum muss man in diesen beiden Ländern ausgehen“, so Merta.
Mit Beton ist also weiter zu rechnen. Er hat aber bekanntlich einen schlechten Ruf, wenn es um die Ökobilanz geht. Merta erklärt, dass Beton an sich ein nachhaltiges Material mit einem niedrigen CO2-Fußabdruck ist. Wenn man ihn mit anderen Materialien vergleiche, sei er nicht „schmutziger“ als diese. „Die Krux an Beton und Zement ist aber die enorme Menge, die hergestellt werden muss“, schildert Merta. Der weltweite jährliche Pro-Kopf-Verbrauch liege nämlich bei über vier Tonnen.
Die CO2-Hauptlast entsteht bei der Zementherstellung – rund acht Prozent der weltweiten Treibhausgasemissionen kommen aus der Zementproduktion: Der Rohstoff Kalkstein muss auf 1.450 Grad erhitzt werden. Dabei entstehen 40 Prozent der Treibhausgas-Emissionen beim reinen Verbrennungsprozess, 60 Prozent werden durch die chemische Reaktion bei der Kalksteinverbrennung freigesetzt.
Zement neu mischen
Die Zementanlagen – vor allem in Österreich – seien bereits äußert effizient.. Da ist laut Merta kaum mehr etwas herauszuholen. Ökologisch gesehen sei also der Hauptansatzpunkt, „wie viel Zement bringt man in den Beton und was für ein Zementtyp bzw. Bindemittel wird dabei verwendet“. „Dort könnte man ökologisch am meisten bewirken. Da sind wir dann im Bereich der Innovationen“, so Merta. Der einfachste Ansatz sei, den Anteil des klassischen, weitverbreiteten Portlandzements im Beton zu senken. Das bedeute eine Optimierung des Materials, also neue Mischungen zu entwickeln, die für diverse Belastungen angepasst werden.
Beton werde üblicherweise bei der Planung von Bauprojekten mit einem Sicherheitswert von 50 massiv überdimensioniert. Bei Stahl oder auch Holz arbeitet man laut der Forscherin dagegen mit Sicherheitswerten von 10 bis 20 Prozent. Hier könnte künftig die additive Fertigung wie z.B. der 3D-Druck dabei helfen, das Material effizienter und in geringeren Mengen – durch niedrigere Sicherheitswerte – einzusetzen. „Damit können die Produktionsprozesse von Betonelementen präzise gesteuert werden. Das Material wird schließlich optimal auf die äußeren Einwirkungen und Lasten (z.B. Gradientenbeton) angepasst eingebaut“, erläutert die Wissenschafterin. Das sei mit den derzeitigen Verfahren (Vorfertigung, Ortbeton) nicht möglich.
Auf der Suche nach Kalkersatz
Ein weiterer Weg der nachhaltig optimierten Betonherstellung führe über die Materialwissenschaften, worin Merta selbst mit ihrem Team tätig ist. Dabei gehe es u.a. darum, alternative Bindemittel zu entwickeln, um den klassischen auf Kalkstein basierenden Portlandzement zu reduzieren bzw. teilweise zu substituieren. Die neuen Produkte müssen idealerweise Eigenschaften wie der klassische Zement aufweisen. Im Fokus der Forschung stehen vor allem alkaliaktivierte Bindemittel (oder Geopolymere), die aus Nebenprodukten anderer Industrien (Hüttensand, Flugasche, Schlacke etc.) durch chemische Aktivierung hergestellt werden können.
Alkaliaktivierte Bindemittel werden laut Merta bereits seit Jahren gut beforscht, alleine die weltweite Verfügbarkeit reicht nicht, um wirklich breit ökologisch wie ökonomisch Wirkung zu entfalten. „Das, was zum Beispiel hierzulande an Hüttensand und Flugasche anfällt, wird bereits von der Zementindustrie aufgenommen. Da passiert schon einiges, es ist kaum noch mehr herauszuholen. Das Potenzial ist ausgeschöpft und die Menge, die man an Portlandzement damit ersetzen kann, fällt nicht wirklich ins Gewicht; optimistisch geschätzt maximal 10 Prozent weltweit “, so Merta.
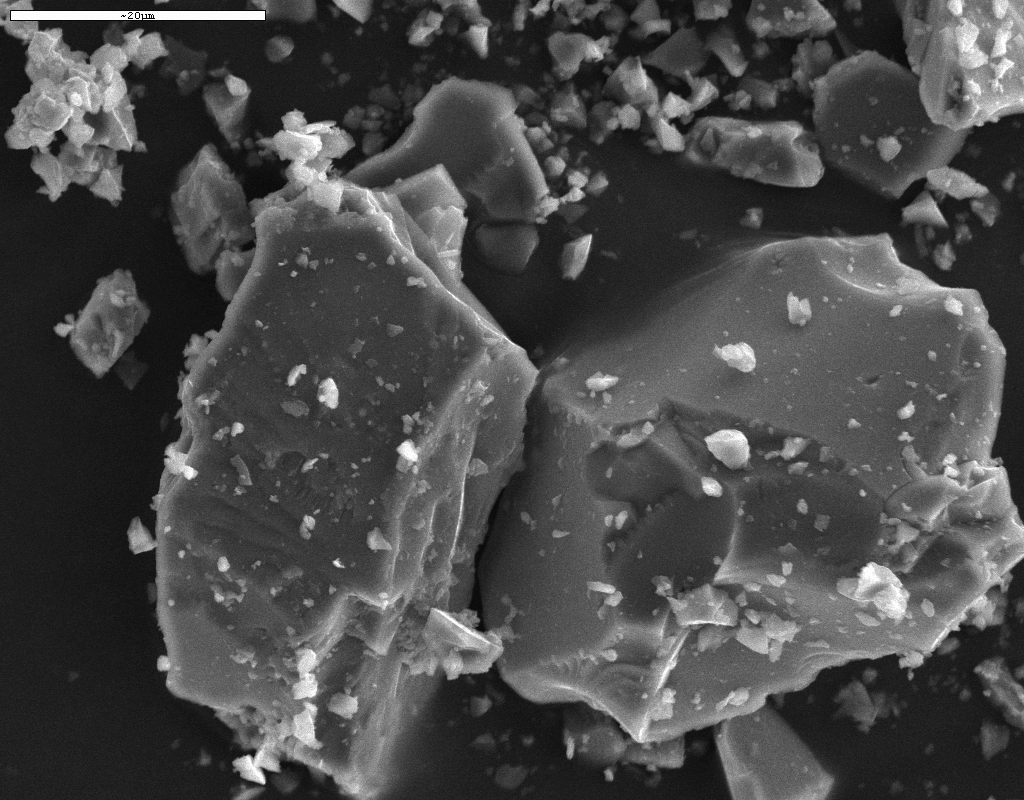
Neuen Ton einbringen
Es heißt somit, Alternativen zu suchen und umzusetzen. In den vergangenen zehn Jahren wurden der Expertin zufolge die Forschungen an neuen und/oder grünen Zementen intensiviert. Es konnten bereits gute Ergebnisse erzielt werden und es gebe erste Anwendungen.
So soll etwa Zementklinker, der gebrannte Bestandteil des Zements, der für die Aushärtung unter Beimengung von Wasser zuständig ist, teilweise durch getemperte (kalzinierte) Tone ersetzt und damit die CO2-Bilanz des Betons verbessert werden. Da die Verbrennungstemperatur von getempertem Ton rund bei der Hälfte von Kalkstein liege, werde insgesamt 30 bis 40 Prozent weniger CO2 ausgestoßen.
Ein weiteres Asset sei, dass es weltweit eine hohe Verfügbarkeit gebe, besonders dort, wo der höchste Beton- und Zementverbrauch anfalle. Laut Merta könnten durch kalzinierte Tone zwischen 40 und 60 Prozent des Portlandzements ersetzt werden. Die Idee wurde an der EPFL in Lausanne unter der Leitung von Karen Scrivener 2004 initiiert und im Rahmen des Projektes LC3 analysiert. Nach der Laborphase seien derzeit die ersten Pilotanlagen im Einsatz. Ein Hochskalieren stehe an.
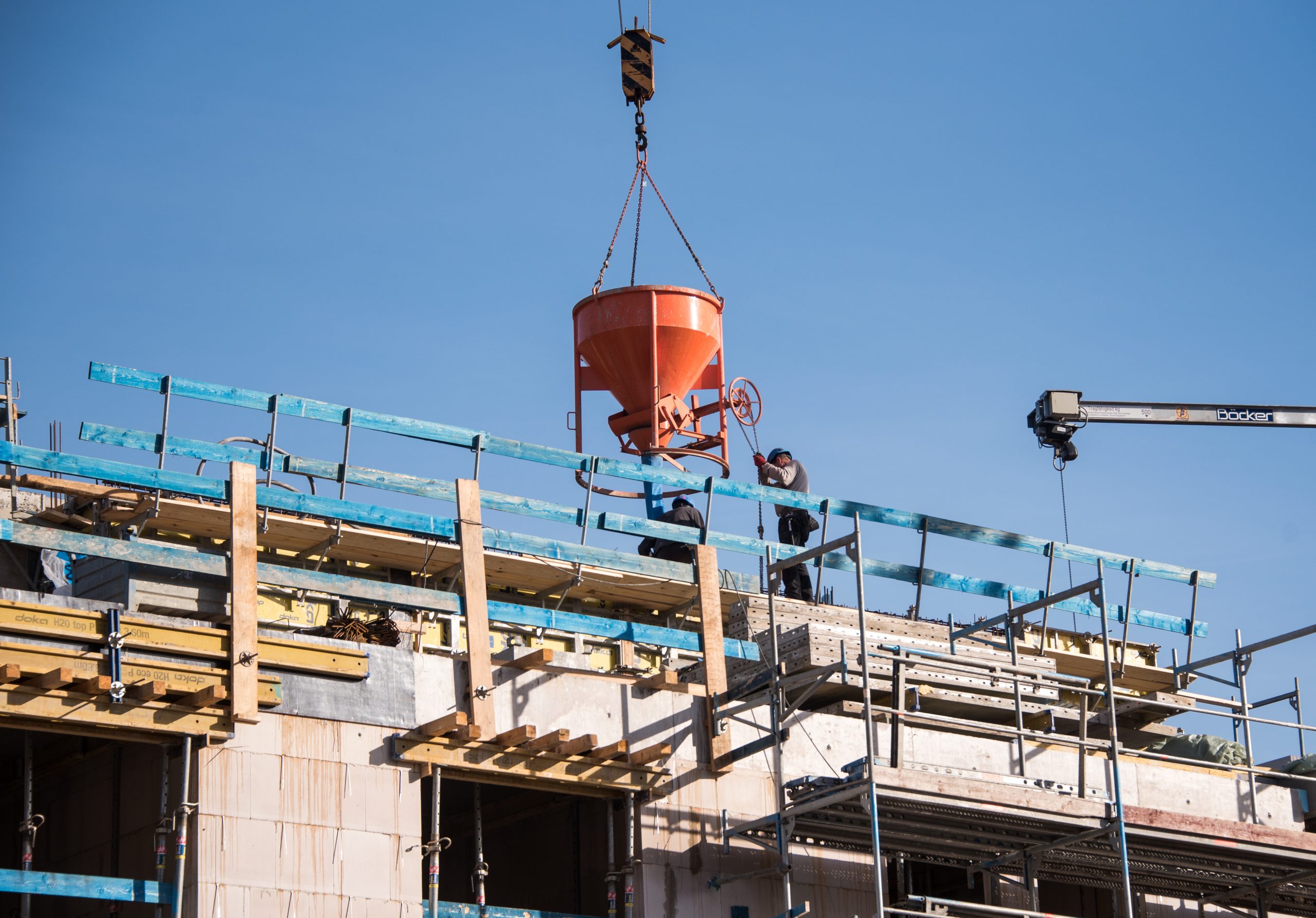
Beton upcyceln
Unter der Leitung von ecoplus Bau.Energie.Umwelt Cluster Niederösterreich arbeitet Merta mit ihrem Team derzeit auf Initiative der Betonindustrie an einem Forschungsprojekt, wo es darum geht, dass noch mehr rezyklierter Beton dem Upcycling zugeführt wird, sprich hochwertig zum Einsatz kommt. Beton soll in der Abbruchhierarchie nicht mehr abgewertet werden, sondern wieder gleichwertig verarbeitet werden. Mertas Team soll in dem vierjährigen Projekt UPcrete – Performance von Recyclingbetonen im Upcycling (https://ildikomerta.com/) untersuchen, welche Möglichkeiten, Herausforderungen und Hürden es gibt. Dabei werden die wichtigsten Einflussparameter untersucht und optimierte Recycling-Betonmischungen entwickelt. Es geht vorderhand darum, eine neue Norm zu schaffen, die es möglich macht, mehr wiedergewonnenen Betonabfall neuen Produkten beizumischen.
Neue Produkte drängen auf den Markt
„In den vergangenen zwei Jahren hat sich sehr viel in Österreichs Beton- und Zementbranche getan“, freut sich auch Joachim Juhart, Leiter der Arbeitsgruppe mineralische Baustoffe am Institut für Materialprüfung und Baustofftechnologie mit angeschlossener TVFA für Festigkeits- und Materialprüfung der TU Graz, im Gespräch mit APA-Science. Der Stand der Dinge sei nämlich, dass die europäische Zementindustrie eine Dekarbonisierungs-Roadmap aufgelegt hat – also Pfade zur CO2-Reduktion in der Zement- und Betonherstellung – und die heimische Zementindustrie folgt diesen Wegen der Roadmap.
In Deutschland seien bereits im Vorjahr derartige Produkte an den Start gegangen, erläutert Juhart. Dahinter liege eine europäische Norm, die noch nicht umgesetzt sei, einige Anbieter seien da aber bereits vorgeprescht. In Österreich werde vermutlich in absehbarer Zeit eine gleichzeitige und flächendeckende Einführung aller Anbieter erfolgen.
Fehlende Normen und Regeln
Juhart fehlt es aber noch an Normen, einem Regelwerk und vor allem einer Vergabepraxis, bei denen CO2-Werte generell berücksichtigt werden. Schon bei der Planung und im nächsten Schritt bei der Vergabe der Aufträge müsste neben dem Preis auch die Qualität hinsichtlich der CO2-Emissionen in die Entscheidung miteinbezogen werden. Das gelte für alle Baustoffe, nicht nur für Beton. Dabei geht es laut dem Wissenschafter um „embodied carbon“, das CO2, das im Material steckt und bei der Produktion anfällt und dann als „Rucksack“ mitgeführt wird.
Ein Hindernis ortet er darin, dass es noch keine einheitliche gemeinsame Datenbasis dafür gibt. Daher komme es bei etwaigen Deklarationen von Fall zu Fall sehr unterschiedlichen, nicht vergleichbaren Angaben. „Es sind zwar mittlerweile Normen geschaffen worden, noch existiere aber keine einheitliche Plattform in Österreich, wo z.B. potenzielle Auftraggeber sich informieren können, mit welchem ‚CO2-Rucksack‘ ist welches Material eigentlich unterwegs“, erläutert Juhart. Er ortet Nachholbedarf, auch die Politik sei diesbezüglich gefordert.
Werden neue Produkte nur nach dem erstmaligen Preis bei der Produktion bewertet ohne ein ‚Bonussystem‘, dann sei es schwer, sie auf den Markt zu bekommen. Anfänglich sollte es da Anschubmaßnahmen geben. Vor allem brauche es ein Bewusstsein bei den Planern und den öffentlichen Bauherren, dass unterschiedliche Baumaterialien unterschiedliche CO2-Lasten aufweisen können.
Fehlende Klasse
„Beton ist nicht Beton, nicht nur bei den Eigenschaften, auch bei der Carbon-Last ergeben sich durch unterschiedliche Beimischungen große Unterschiede“, so Juhart. Der Parameter Treibhauspotenzial werde noch kaum in der Planung berücksichtigt.
Das gelte auch für die Klassifizierung von Beton. „Es gibt Klassen für die Festigkeit, die Dauerhaftigkeit, sogar die Verarbeitbarkeit für verschiedene Anwendungen, aber es gibt keine Klasse für das Treibhauspotenzial“, schildert Juhart. Würde man derartiges schaffen, könnte man Planer wie Bauherren aber auch Auftraggeber unterstützen, da es als Gütekriterium wahrgenommen würde – schwarz auf weiß. Das sollte dann über sämtliche Baumaterialien – nicht nur Beton – hinweg vergleichbar sein, wiederholt der Materialwissenschafter.
Das Forschungsfeld
„Wir haben in den vergangenen Jahren Ansätze bei der Betonherstellung, nicht beim Zement, verfolgt“, umreißt Juhart sein Forschungsfeld. Dabei sei es um die Optimierung von Betonprodukten in Zusammenarbeit mit Betrieben aus der Industrie gegangen. „Wir konnten Betonrezepturen entwickeln, die deutlich CO2-ärmer sind als alles, was derzeit ausgeliefert wird“, schildert Juhart.
„Prototypisch haben wir dabei bereits gezeigt, dass im Beton bis zu 25 Prozent weniger CO2 stecken könnte“, ergänzt er. Aus verschiedenen Gründen komme es aber noch zu keinem flächendeckenden Einsatz. Hauptsächlich daher, dass es, wie bereits erwähnt, bei Ausschreibungen kein Kriterium sei. Vielen Bauherren sei es auch zu riskant, neue Baustoffe, oder neu adaptierte Baustoffe einzusetzen, wo es noch an Langzeiterfahrungen fehle. „Das scheint sich jetzt aber zu ändern . In die Branche ist Bewegung gekommen“, ist Juhart für die Zukunft zuversichtlich.
„Bauherren sind natürlich daran interessiert, dass die Dauerhaftigkeit des Baumaterials gewährleistet ist. Sie möchten, dass Bauwerke im Hochbau mindestens 50, im Infrastrukturbau mindestens 100 Jahre halten. Auch auf diesem Feld sind wir aktiv“, erklärt der Betontechnologe. Dabei soll mittels beschleunigten Dauerhaftigkeitsprüfungen gezeigt werden, dass Betonmischungen mit alternativen Rohstoffen die Ansprüche des Marktes und der Zuverlässigkeit sowie Beständigkeit nach Normen erfüllen. „Das ist aufwendig, es bedarf an Investitionen, die Prüfkosten müssen übernommen werden. Das sind Aufwände, die von der Wirtschaft oft nicht ohne weiteres gemacht werden“, erläutert der Experte, warum es oft viel Zeit braucht, bis neue Produkte in der Praxis ankommen. „Technisch ist viel mehr möglich, als praktisch gemacht wird“, fasst er zusammen.
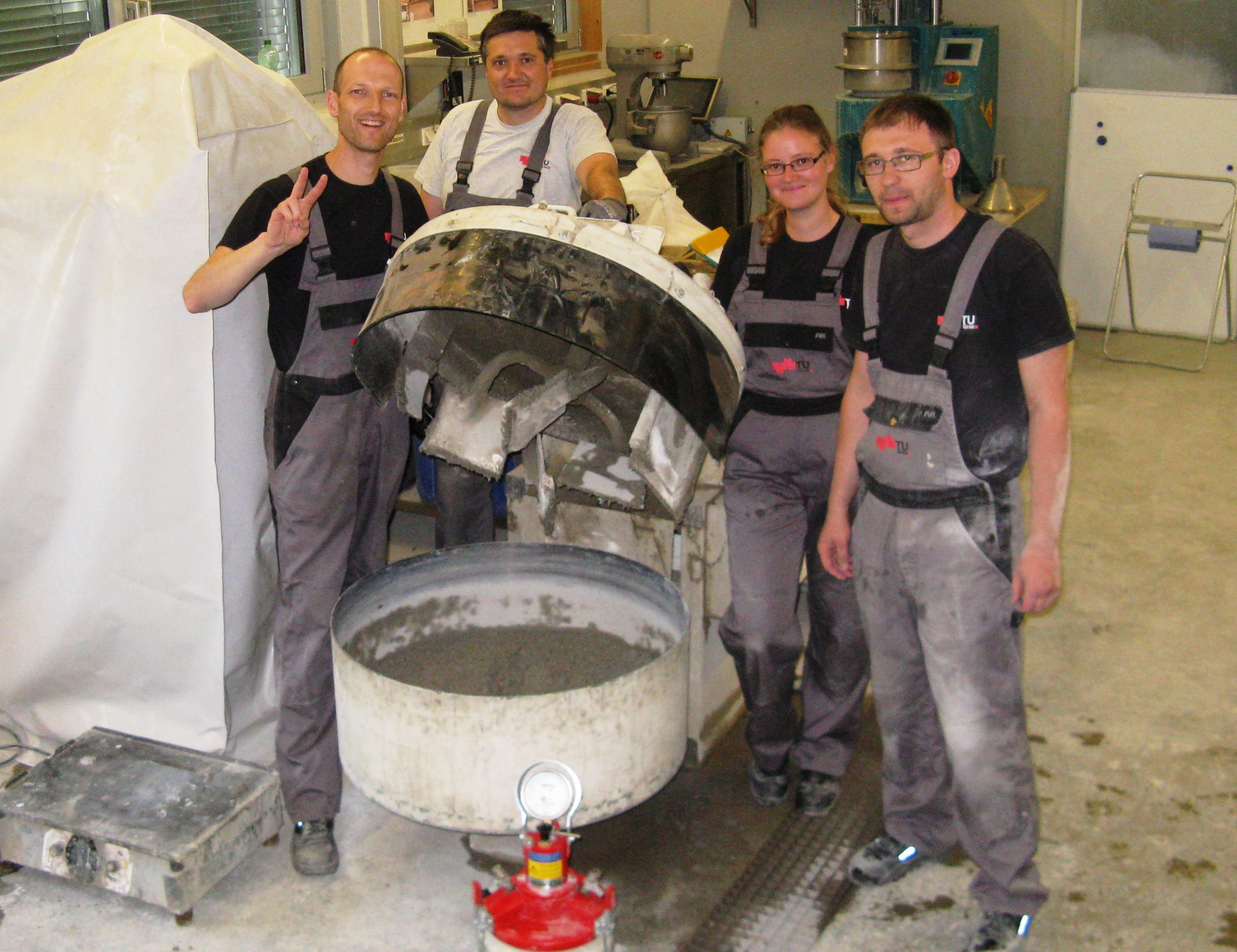